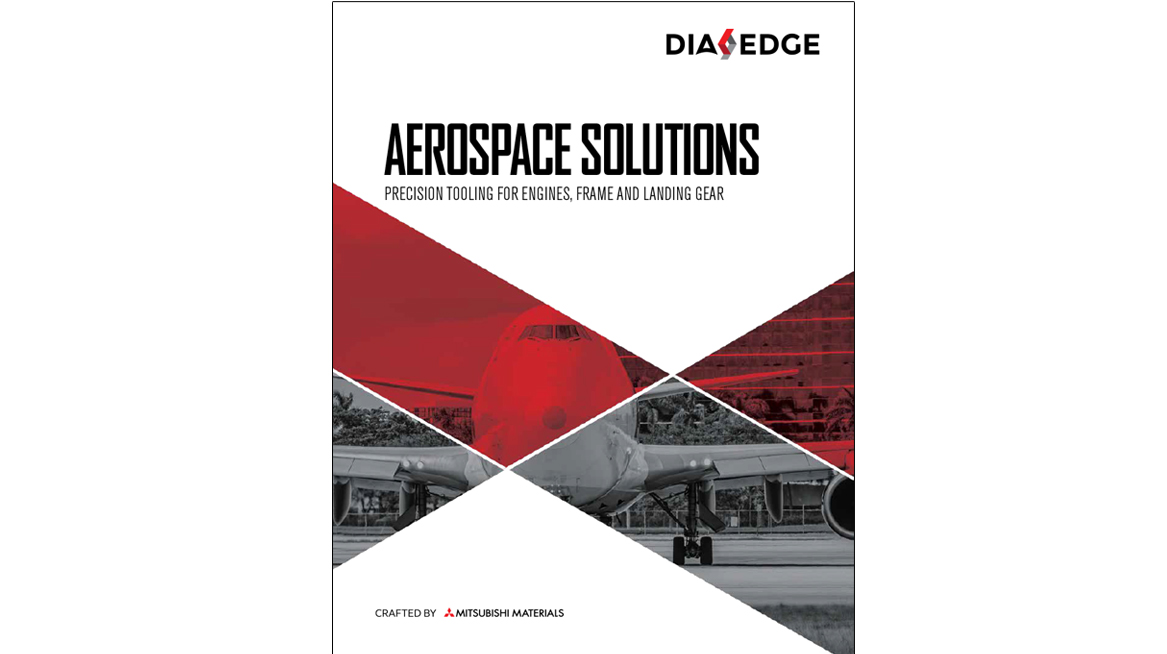
Aerospace
AIR FRAME
CFRP Wing
1. Drilling
MCC Drill: A 90° point angle is used to reduce thrust when drilling, this prevents delamination and also improves hole tolerance.
MCA Drill: A unique flute design is employed to prevent the aluminium chips from damaging the finish of the CFRP section thus reducing the gap in hole size between the aluminium and CFRP section.
2. Trimming
Cutting tool life is usually extremely short because of the high strength of carbon fibre, additionally, delamination and burring easily occur during cutting, thus it is effective to use a tool that applies coating with high wear resistance.
The DFC end mills reduce burrs and delamination due to a CVD diamond coating technology in combination with an optimized tool geometry, thereby achieving a long tool life and high-quality machining.
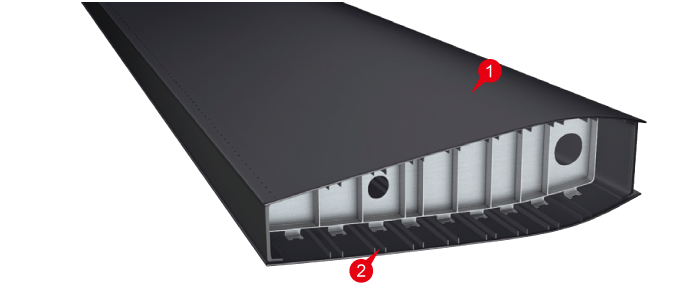
Wing Rib
1. Face Milling, Pocket Milling
Milling of rib-type components involves removing large volumes of over 90%. Thus, highly efficient machining at high speed is required to reduce cost.
The AXD series achieves low cutting resistance without lowering the insert edge strength due to a helical flank and optimized relief angle. Additionally, the convex cutting edge allows good chip removal, resulting in high-speed and high-efficiency machining.
The use of MP9120 grade is highly effective in super-high-speed cutting.
The ALIMASTER series achieves good chip removal due to the unique cross-sectional shape of the flute geometry shape. This enables high-speed and high-efficiency machining.
The head of exchangeable head end mills iMX for machining of aluminum alloy prevents welding due to the large rake angle and the mirror treatment for improved efficiency.
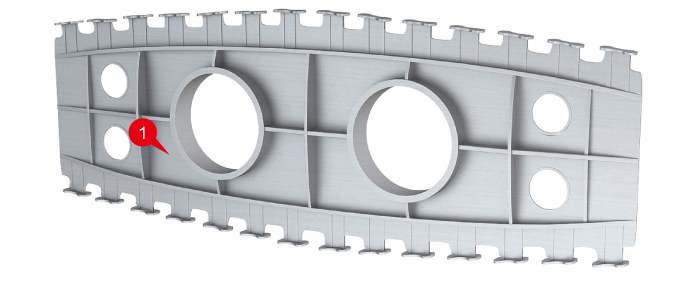
Hinge
1. Side Milling, Rough Pocket Milling
When rough machining titanium alloy, chipping and abnormal damage of the cutting edge easily occur if low-rigidity tools are used. Using high-rigidity tools and low-cutting resistance inserts is recommended. Stable machining is possible because the VFX series has a high rigidity design and cutting resistance is lower due to the convex curve cutting edge and the V-formation of the clamping face.
2. Drilling
Drilling performance in 15-5PH precipitation hardening stainless steel. Abnormal damage such as chipping and fracture on the cutting edge occurs easily because of the high strength of 15-5PH which is often used for an aircraft component. The MMS drill series enables stable machining due to an excellent coating technology in combination with an optimized tool geometry.
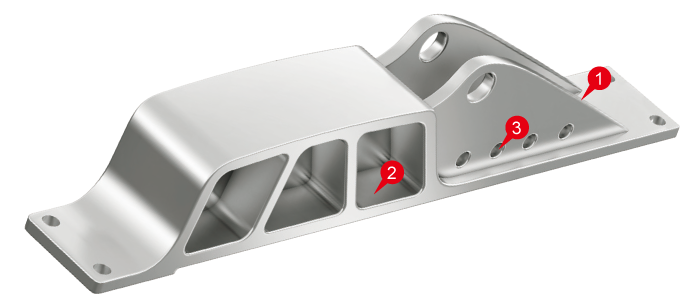
Flap Track
1. Face Milling, Side Milling
There is a concern about chipping and fracture during high-speed roughing because cutting resistance varies in the process of generating a saw-toothed chip in roughing of titanium alloy. The combination of newly developed MP9130 grade with excellent wear resistance due to Multi-layering of the coating and JL breaker with low cutting resistance enables stable high-speed roughing.
1. Side Milling, Pocket Milling
ARP Series: When rough machining of titanium alloys due to the type of chips generated problems relating to chipping and fracturing are common. The ARP series inserts are available in 3 breaker geometries and with the new MP9130 tool grade. This combination results in stable machining when carrying out roughing and finishing applications of titanium alloys.
Coolstar Series: When machining titanium alloys due to the fact that the thermal conductivity is low heat generated during machining localizes around the cutting edge. This results in welding problems and as such it is necessary to prevent heat generation and to remove the chips effectively. The Coolstar series is designed with multiple through-coolant holes in the flutes of the tool. This ensures effective cooling and improves chip evacuation.
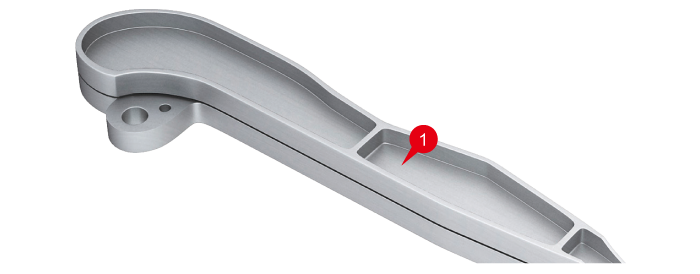
ENGINE
Combustion Casing
1. Helical Cutting, Profile Milling
Ni-based difficult-to-cut heat-resistant alloys such as Inconel 718 soften at temperatures exceeding 800ºC. At these temperatures, difficult-to-cut materials become easier to machine because their bearing and tensile strengths are lowered. Ceramic end mills can work effectively at these high temperatures and self-generate the heat required to soften the machined material through ultra-high feeds and speeds.
2. Machining of Upper Surface Resistance Insert of Protuberance
When machining Ni-based alloys which have low thermal conductivity and are subjected to work hardening, well-balanced cutting edge, and superior coating grade are required. APX series extends tool life greatly due to optimized cutting edge geometry and new grade insert.
3. Drilling
The key is how to cool a cutting edge when drilling Ni-based alloys. It is possible to extend tool life greatly by using a solid carbide drill that employs TRI-Cooling through coolant technology with a high-pressure coolant supply.
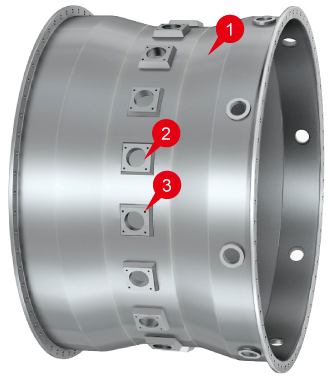
Blisk
1. Finish Profile Milling
When machining Ni-based alloys which have low thermal conductivity and are subjected to work hardening, well-balanced cutting edge, and superior coating grade are required. The latest SMART MIRACLE vibration control ball nose end mills have variable pitch geometry with newly designed radius-cutting-edges to reduce vibration.
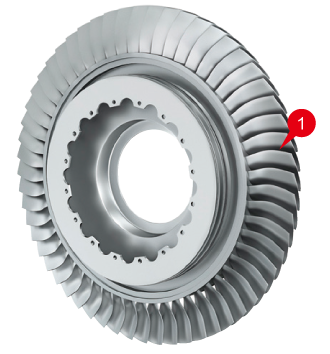
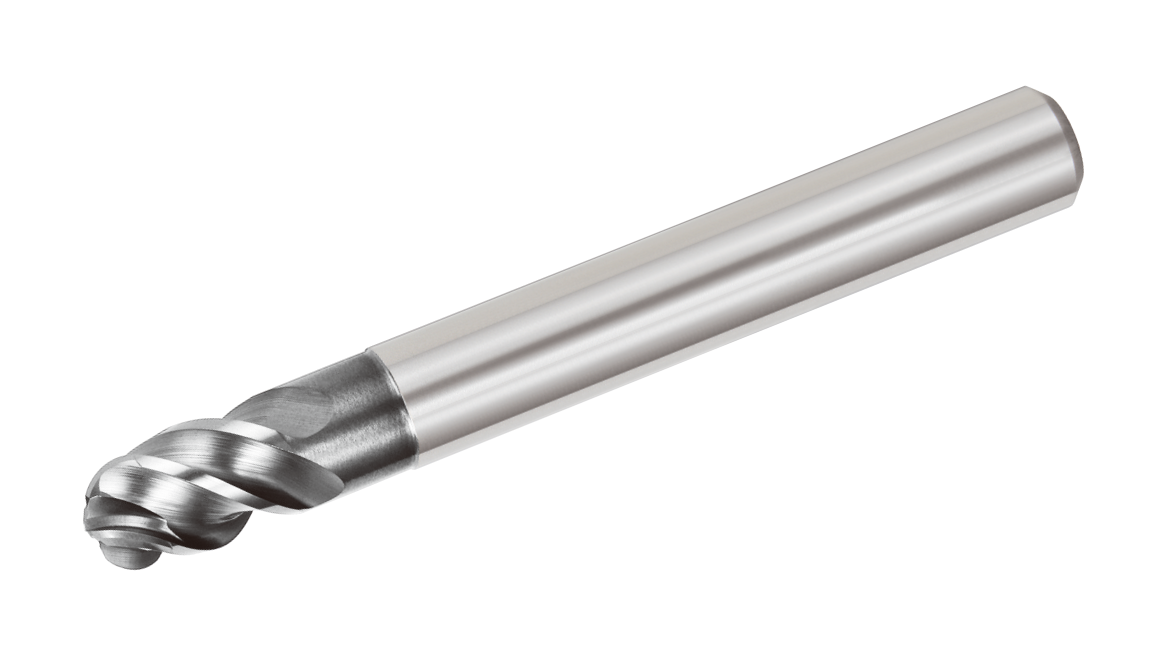
1. SMART MIRACLE Vibration Control Ball Nose End Mill
Vibration Control End Mills for Machining Difficult-to-Cut Materials
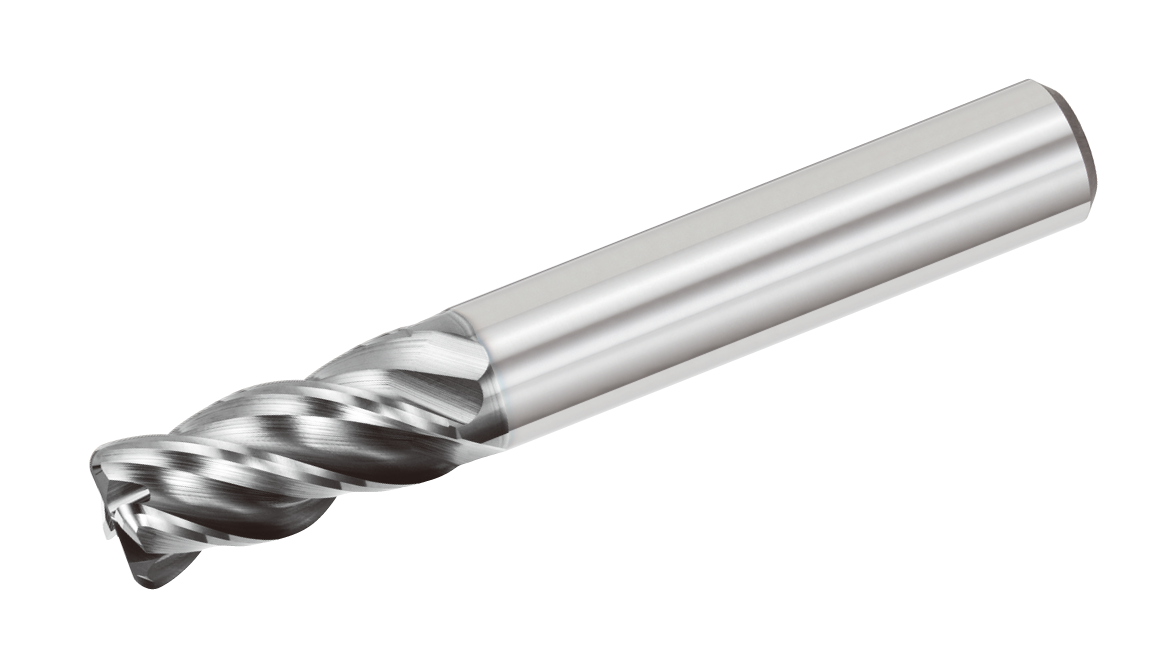
1. SMART MIRACLE End Mill Series
Vibration Control End Mills for Machining Difficult-to-Cut Materials
Fan Casing
1. External, Face, and Internal Turning
A rough estimate of the tool life is 120 minutes at 80m/min and 60 minutes at 120m/min when finish-machining titanium alloy. Non-coated grades are the first recommendation.
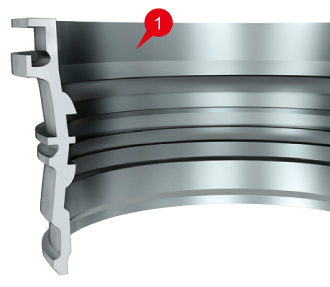
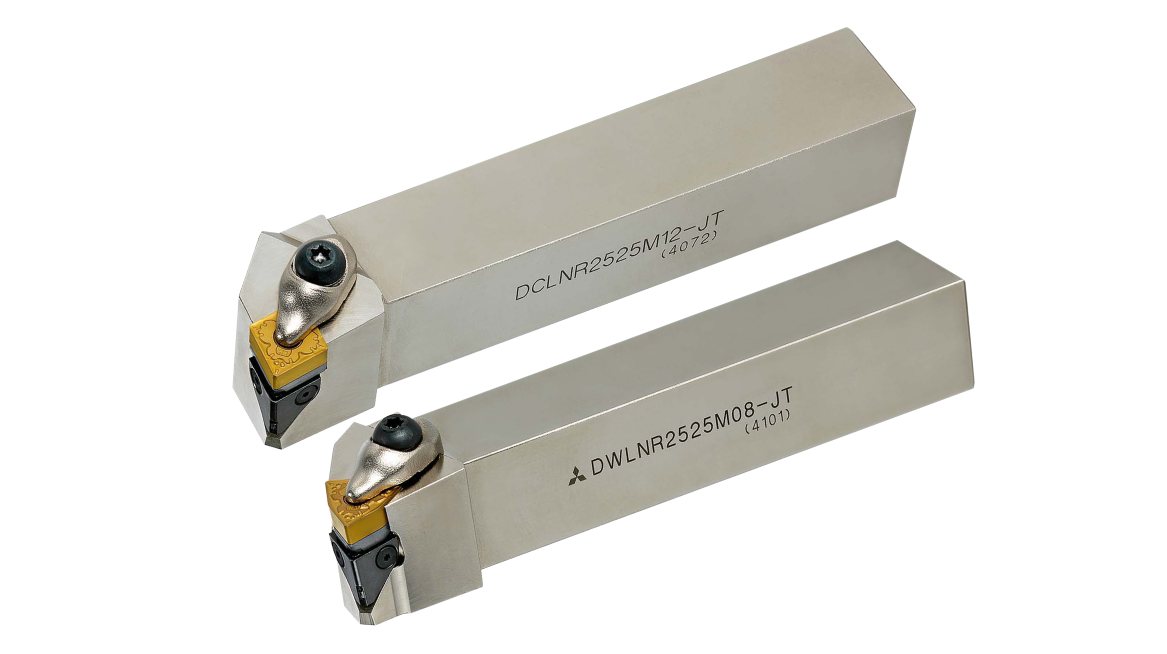
1. JT Holder
Internal Lubrication Bite Holder
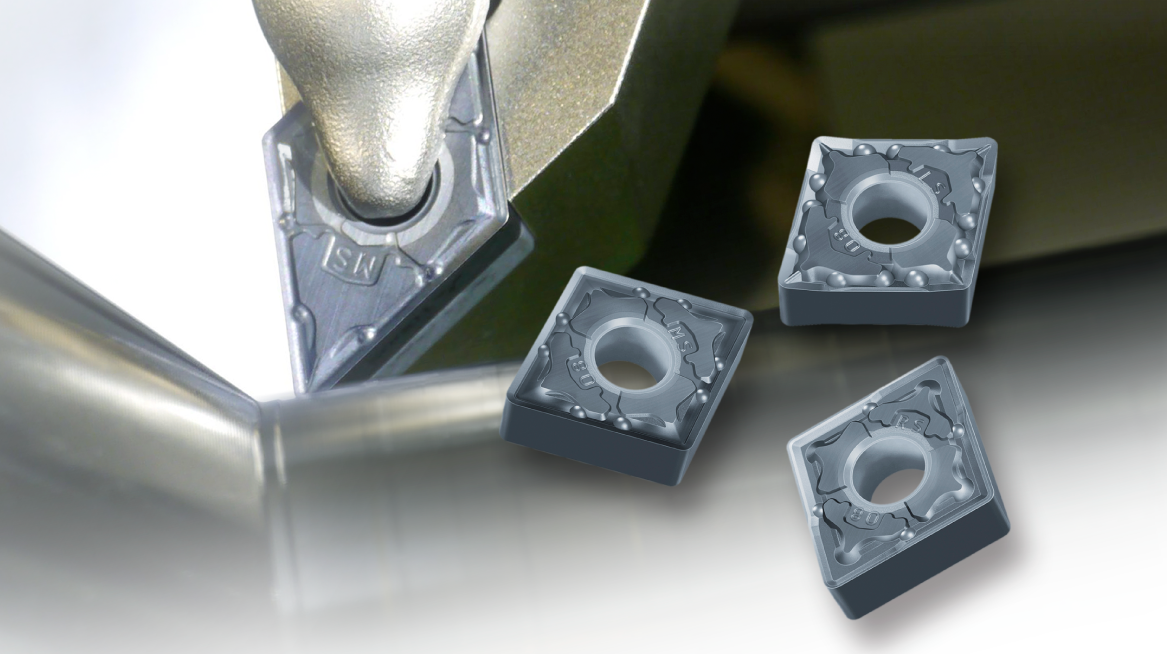
1. LS/MS/RS Breaker MP/MT9000 Series
ISO Turning Inserts for Difficult-to-Cut Materials
Shaft
1. External, Face, and Internal Turning
When rough machining engine shafts are made from maraging steel, the use of grades for hard materials such as VP05RT through the use of the CBN is recommended.
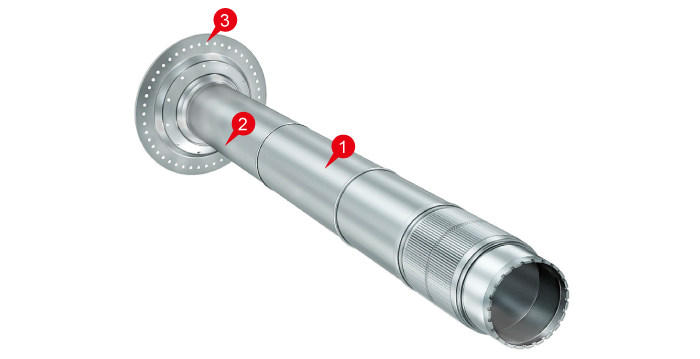
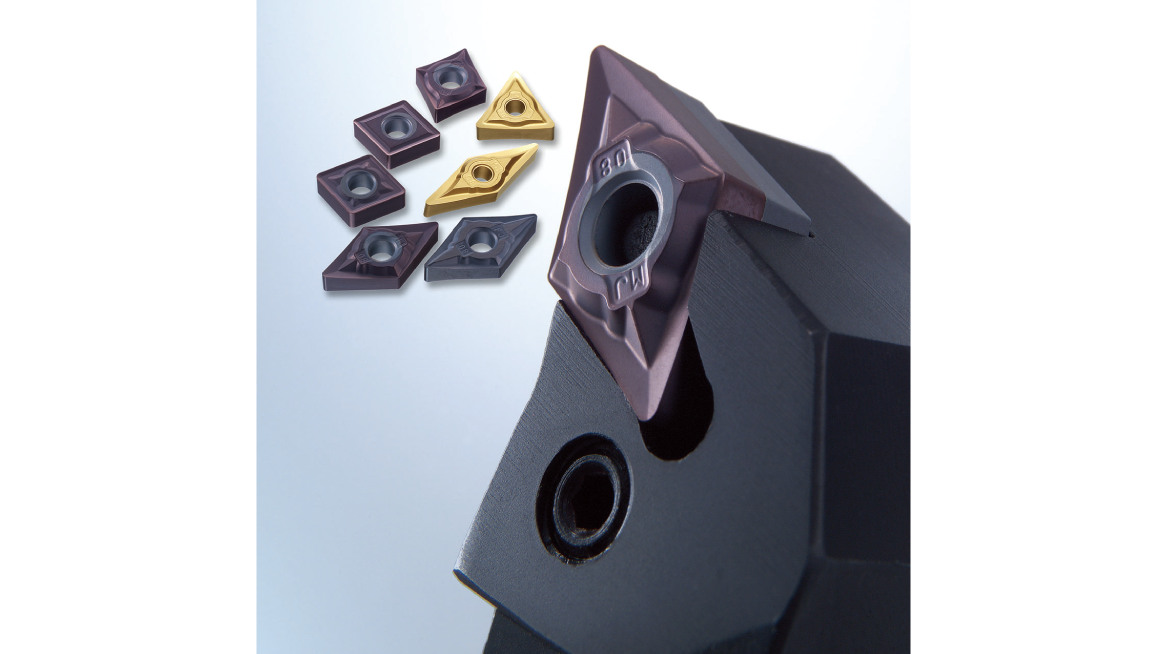
2. FJ/MS/GJ Breaker VP05RT/ VP10RT
Special Breakers for Difficult-to-Cut Materials
LANDING GEAR
Shaft
1. Drilling
Adhesion and concentration of heat on the cutting edge occur easily during the drilling of titanium alloys because of the low thermal conductivity thus it is important to remove heat on the cutting edge efficiently and to evacuate chips smoothly. MNS drill provides excellent cooling performance and chip discharge performance due to the arrangement of unique coolant holes and the employment of optimum groove shape, thereby achieving stable machining even when drilling titanium alloy.
2. Finish Profile Milling
When profile machining titanium alloy, chipping, and abnormal damage to the cutting edge can occur and vibration is easily generated. The use of a tool that is designed for vibration control is effective. The latest SMART MIRACLE vibration control ball nose end mills have variable pitch geometry with newly designed radius-cutting-edges to reduce vibration.
3. Rough Milling
When rough machining titanium alloy, chipping and abnormal damage of the cutting edge easily occur if low-rigidity tools are used. Using high-rigidity tools and low-cutting resistance inserts is recommended. Stable machining is possible because the VFX series has a high rigidity design and cutting resistance is lower due to the convex curve cutting edge and the V-formation of the clamping face.
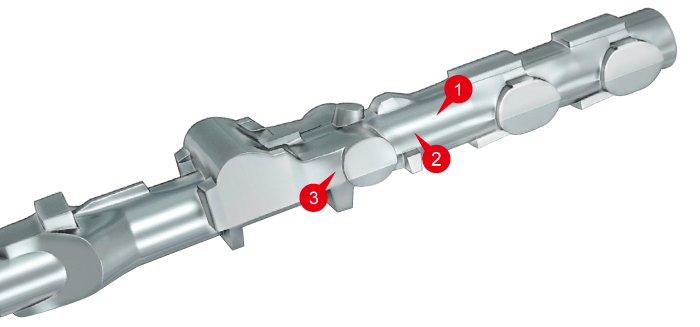
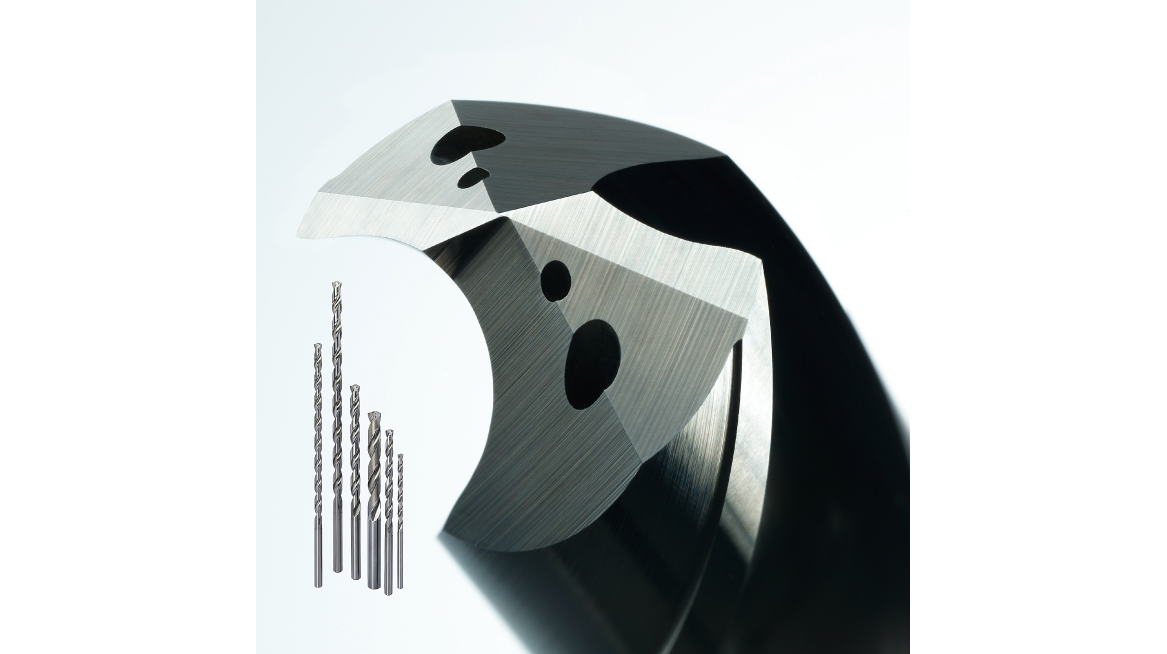
1. MNS Drill
Solid Carbide Drill for High Efficiency Machining of Aluminium Alloys
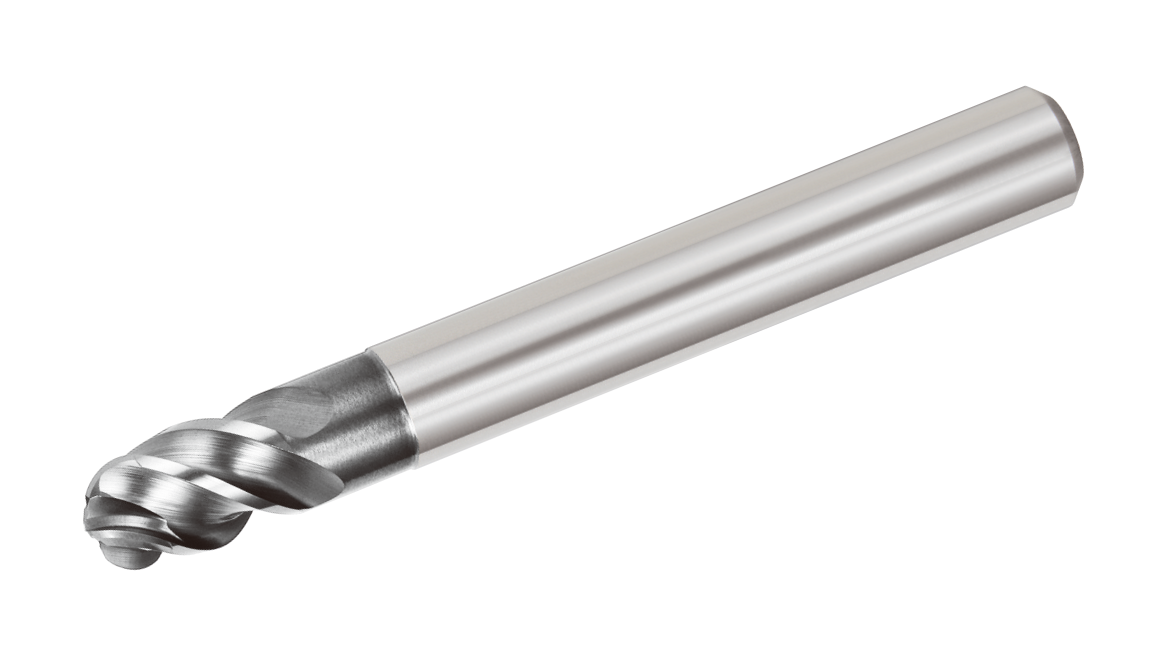
2. SMART MIRACLE Vibration Control Ball Nose End Mill
Vibration Control End Mills for Machining Difficult-to-Cut Materials
Download Contents
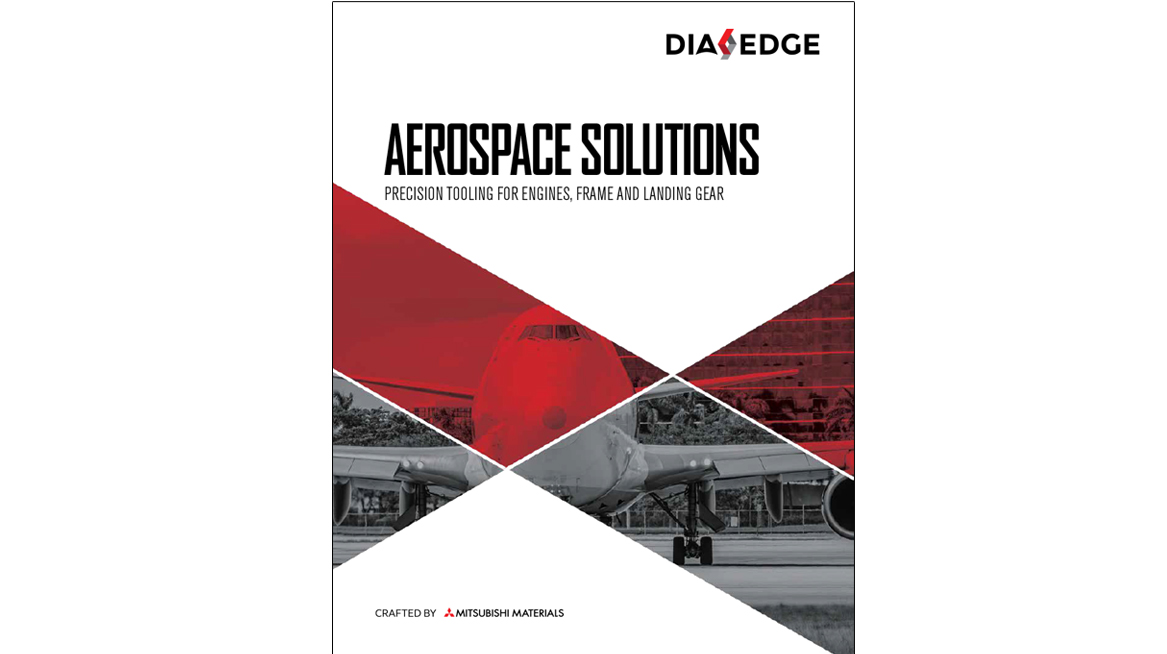
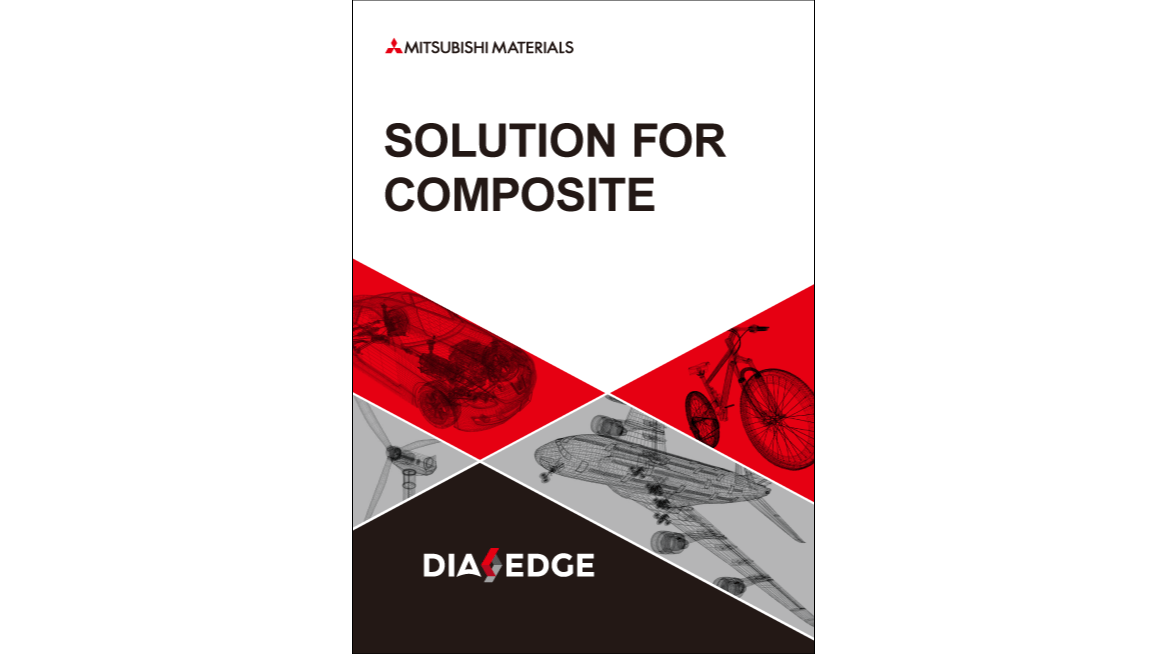