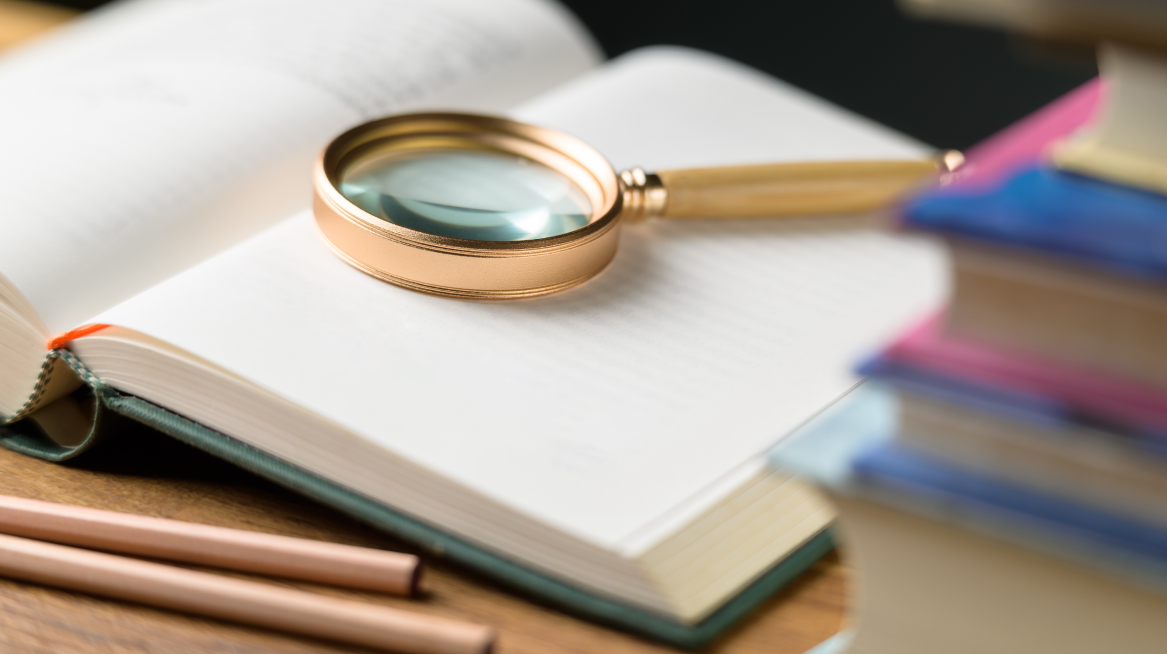
高能率加工を可能にする薄膜技術
Thin films and coatings technologies for high efficiency machining
長田 晃*
Akira OSADA
1. はじめに
鋼や鋳鉄,非鉄金属等の各種金属材料を加工する切削工具には,超硬合金やセラミックスなどの各種硬質材料が使用されているが,中でも現在最も多く使用されている材料は,硬さと強度をバランス良く兼ね備えた超硬合金およびその表面に硬質セラミックス膜を被覆したコーティング超硬合金である。コーティング超硬合金は,超硬合金の表面をチタンの炭窒化物(TiCN)やチタンとアルミニウムの窒化物((Ti,Al)N),酸化アルミニウム(Al2O3)などの硬質セラミックスの薄膜で被覆したもので,数μm~20μm 程度の薄膜により工具寿命が数十倍以上に向上する。実用上は,工具寿命は被削材の種類や加工条件に大きく左右され,切削工具の高性能化は高能率加工のための切削条件向上や被削材の難削材化などに活用される場合が多い。つまり切削工具のユーザーは工具寿命の延長よりもより高能率で加工を行うことを目指しており,それを実現する工具材料としてコーティング超硬合金が長年にわたり重要な役割を果たしてきている。このことを裏付けるデータとして,図1 に刃先交換式の工具に使用されるインサートの国内における生産量の推移を示す1)。2008年のリーマンショックの影響を強く受けてはいるが,中長期的にみるとその生産個数は10年前と比較し倍増していること,材料比率ではコーティング超硬合金の比率が年々増加し約70%に達していることが分かる。この傾向は今後も続いていくと考えられる。
コーティング超硬合金に使用される薄膜技術には,化学蒸着(CVD:Chemical Vapor Deposition )法と物理蒸着(PVD:Physical Vapor Deposition)法があり用途に応じて両者が使い分けられてる。歴史的にはCVD法によるコーティング超硬合金が古く,1969年に実用化され,PVD法によるコーティング超硬合金の実用化はそれより10年以上後になる。このため,初期の使用量拡大はCVD法による主としてインサートへの薄膜技術の開発や改善によるものが多い。これに対し,PVD法は主にCVD法の適用が難しいドリルやエンドミルなどの軸物工具への応用から始まり,その使用範囲を広げて行った。1990年代には,CVD法では中温CVD(MT-CVD:Moderate Temperature CVD)法によるTiCN が2),PVD法ではアークイオンプレーティング(Arc Ion Plating)法による(Ti,Al)N が,それぞれの用途で幅広く応用され,コーティング超硬合金の使用領域拡大と使用量の増加に大きく貢献した。これは,それぞれの成膜法の他方に対する欠点を大幅に改善したことによる。MT-CVD法によるTiCN は,PVD法と比べた場合のCVD法の欠点である強度の低下を低温化により改善し,アークイオンプレーティング法による(Ti,Al)N は,PVD法で成膜が難しいAl2O3に変わる耐酸化性に優れた薄膜材料として,従来はCVD法が主であったインサートでもその使用量を増大させた。その後も各種の薄膜技術が開発,改良され新製品に応用されることで,加工現場での高能率化や結果としてのコスト低減に寄与してきている。
ここでは,このような切削工具用の薄膜技術および材料について,その開発の歴史を振り返るとともに,当社中央研究所における研究・開発内容について2000年代以降を中心に紹介,解説する。
* 薄膜材料研究部長
ものづくり・R&Dレビュー 第 1 号(2012)掲載
つづきはPDFファイルをご覧ください
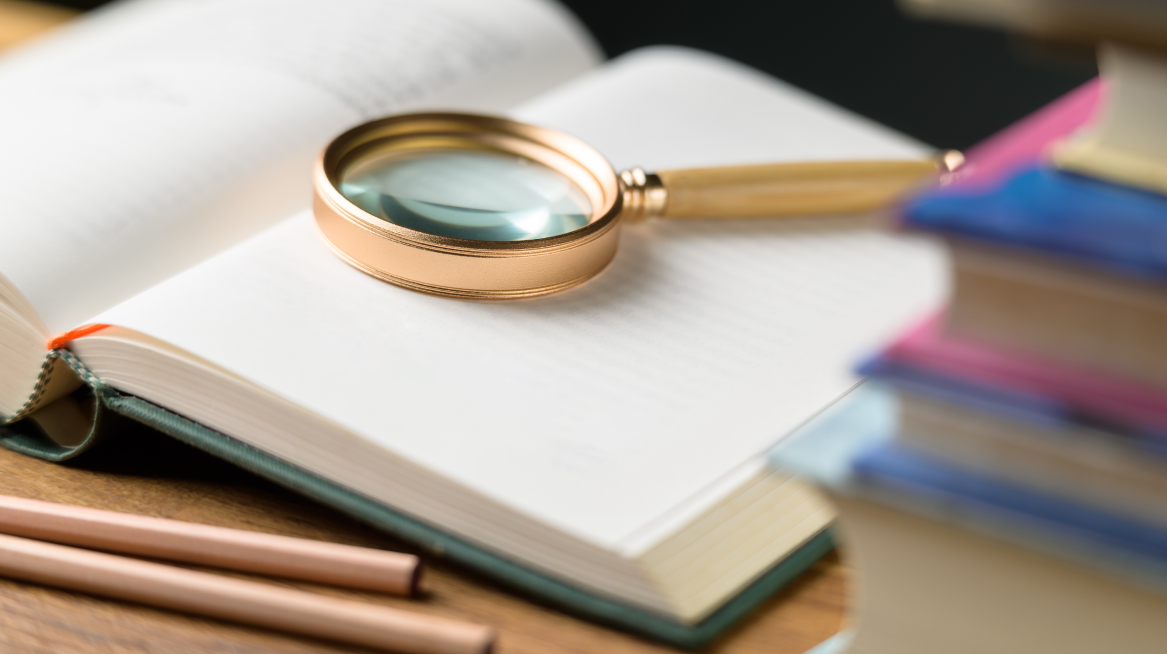