MS9025
PVD Coated Grade for High Precision and Small Parts Machining
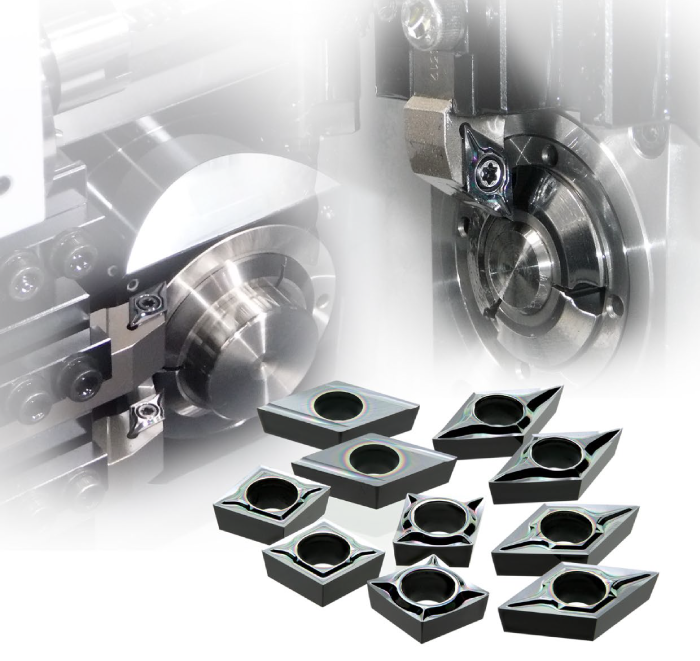
Improved Cutting Edge Delivers
Next Generation Small Parts
Machining
Improved Cemented Carbide
Thermal conductivity has been improved by optimising the grain size and therefore reducing the boundary contact between the WC particles. This optimisation reduces the temperature of the cutting edge during machining.
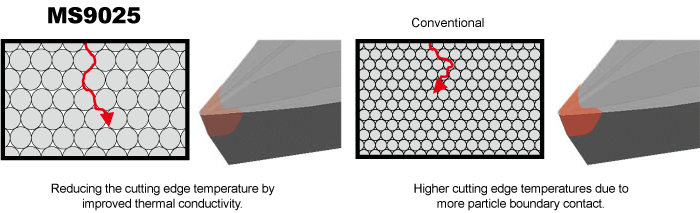
Smooth Surface of The Coating
The even surface of the coating has been achieved by first making the the carbide substrate smooth then by promoting straight growth of the coating crystals. This leads to excellent welding resistance.
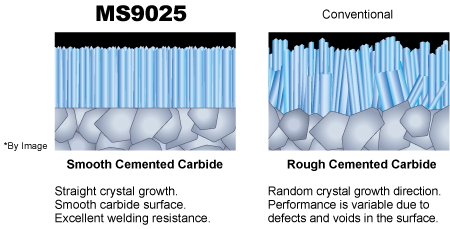
New Technology - Controlled Vibration of the Cutting Tool
Using new machine technology to deliberately vibrate the tool in relation to the cutting direction is an
effective way of breaking chips.
This reduces production costs by reducing chip entanglement.
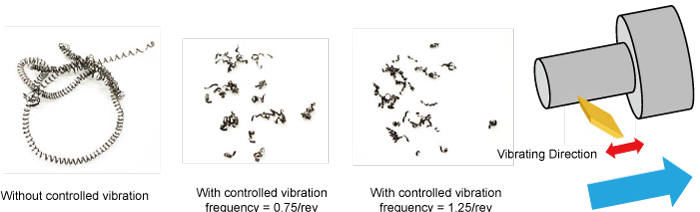
Challenges of controlled vibration machining:
Compared to standard machining there is a greater chance of edge chipping due to the extra stress on
the cutting edge and also because of the impact of work hardening.
Benefits of using MS9025 for Controlled Vibration Machining
- Excellent fracture resistance due to the inherent toughness of the base material.
- Effectively suppresses boundary wear damage during machining of difficult-to-cut materials. This is
achieved by the optimised cemented carbide grain size that reduces thermal conductivity and heating
of the cutting edge.
After 500 passes at 15m per pass
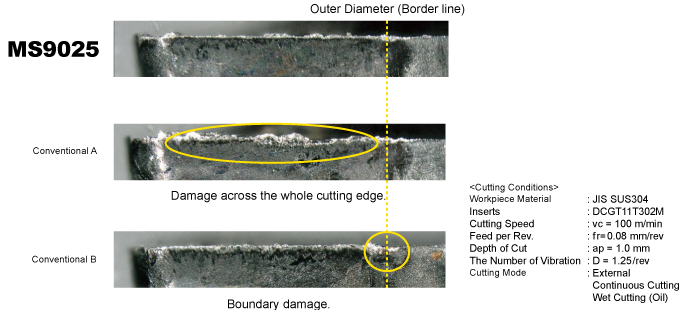
High Al-rich(Al,Ti)N Single Layer Coating Technology
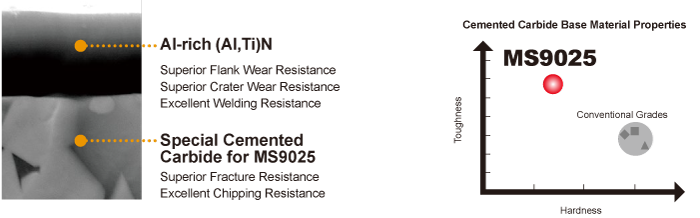
High Al and Conventional Coating Comparison
The high Al-rich (Al,Ti)N single layer coating provides stabilization of the high hardness phase and succeeds in dramatically improving wear, creater and welding resistance.
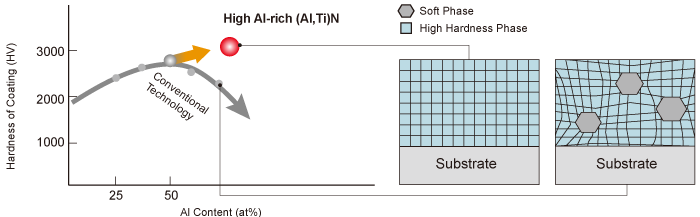
Extremely High Quality Cutting Edge
Technology that provides superior dimensional stability and reduces burrs.
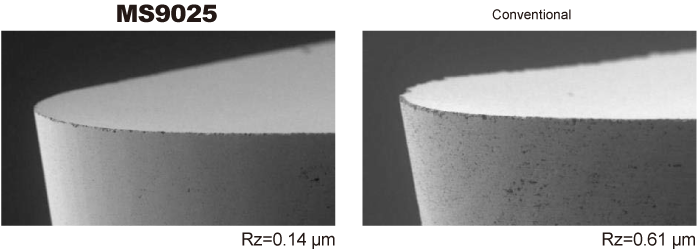
Cutting Performance
Stainless Steel SUS440C, Wear Resistance Comparison
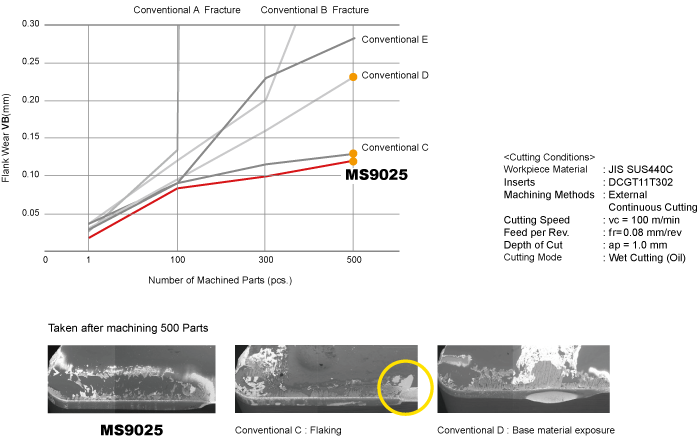
Application Examples
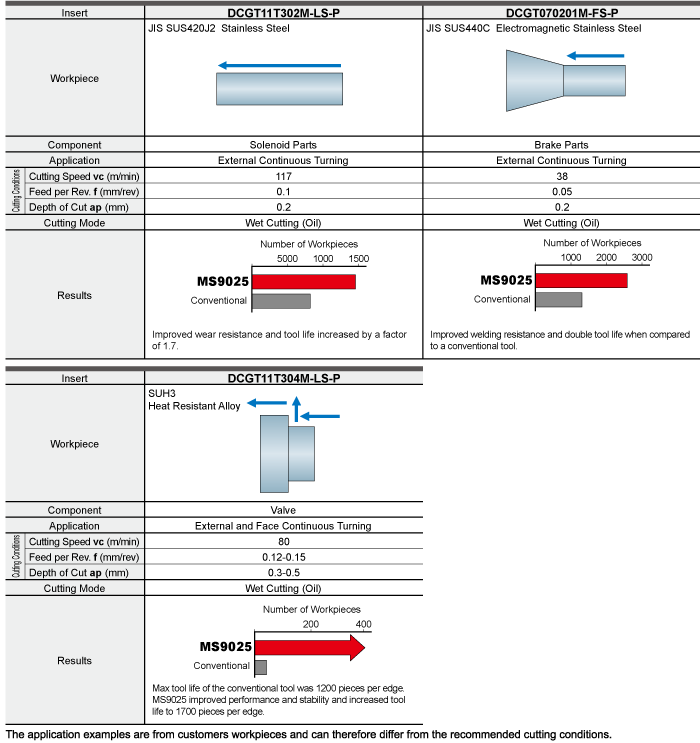
Technical consultation from here
24/7Contact form