MICRO-MINI TWIN
Boring Bar for High Precision and Small Parts Machining
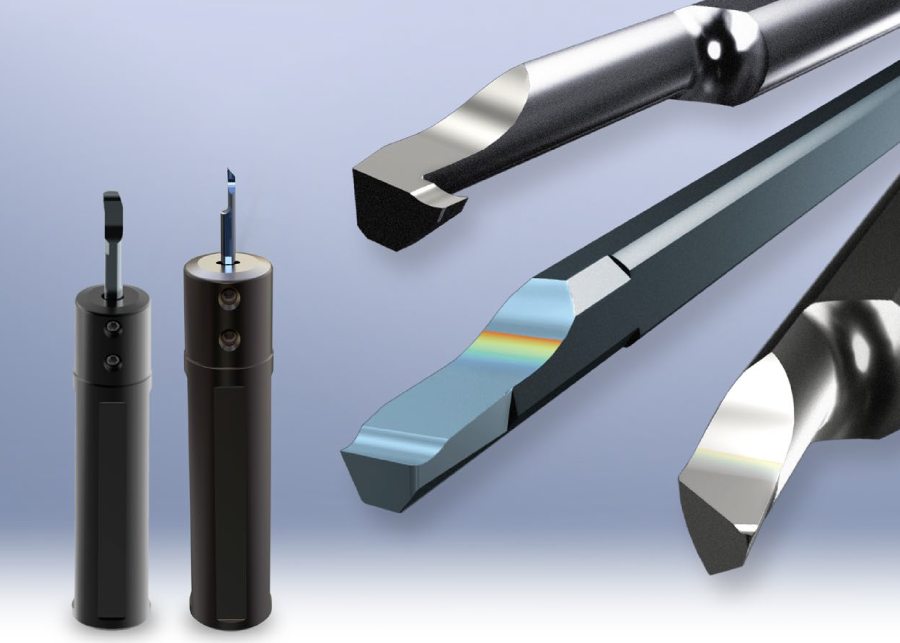
Ideal for small-diameter boring of general and stainless steel.
Double Ended Cutting Edges
A cutting edge on each end provides reduced tooling costs.
Wide Range Available
The multi functionality of the Micro-Mini Twin enables a wide application range that covers boring, grooving and threading and is available with or without a chipbreaker.
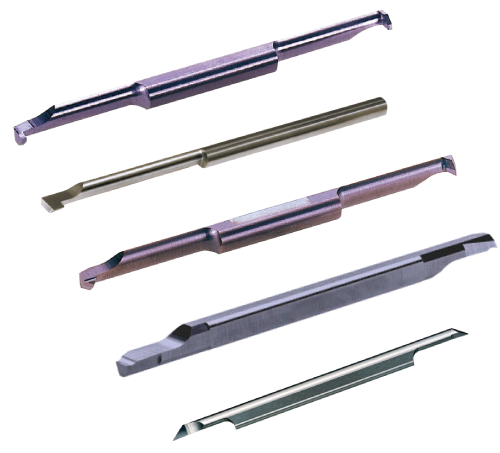
・Boring
Minimum Cutting Diameter : φ2.2mm~
RE : 0.05, 0.1, 0.15, 0.2
・Grooving
Minimum Cutting Diameter : φ3mm~
・Threading
Minimum Cutting Diameter : φ3mm~
・Copying
Minimum Cutting Diameter : φ3.5mm~
Available With or Without a Chip Breaker
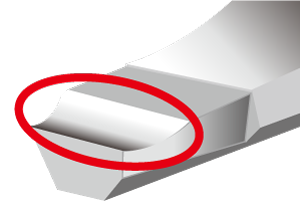
With Chip Breaker
The wide chip breaker aids in reducing cutting resistance.
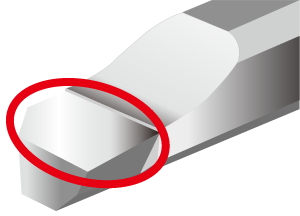
With Out Chip Breaker
Polished rake face to prevent chip welding.
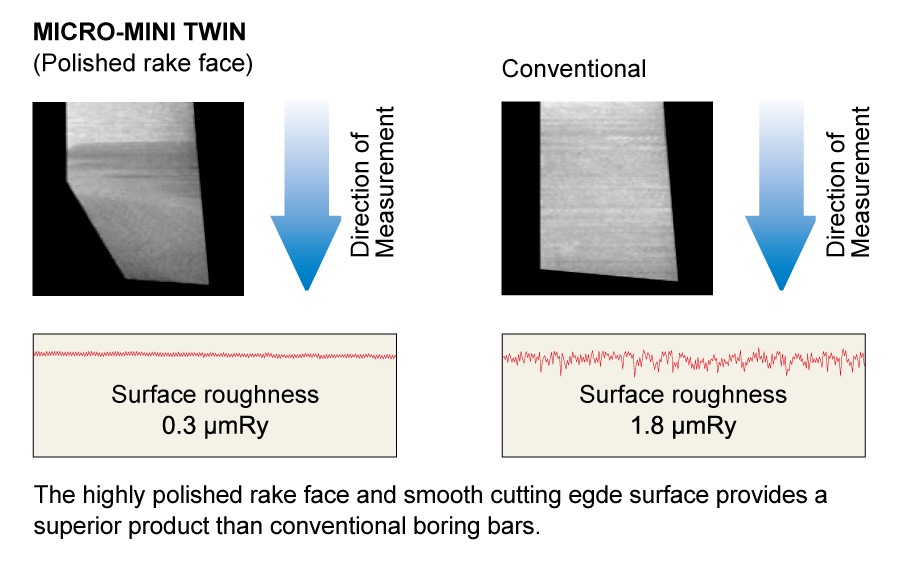
Cutting Performance
Polished Rake Face
Machining of Stainless Steel
The polished rake face prevents chip welding and provides an excellent surface finish.
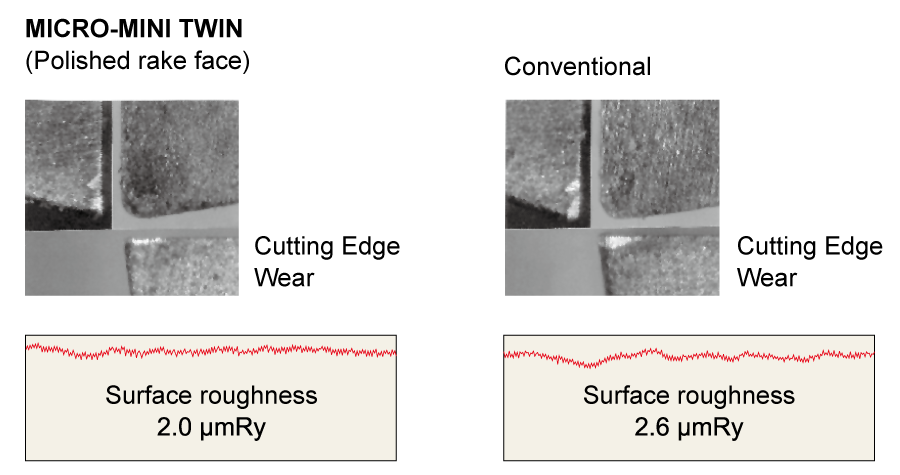
Workpiece Material : SUS304 Tool : CB05RS,VP15TF
Cutting Speed : vc=100m/min Feed per Rev. : fr=0.02mm/rev
Cutting Depth : ap = 0.1 mm Cutting Mode : Wet Cutting
Sleeve
A sleeve specially designed the MICRO-MINI TWIN for optimum use on Swiss-Type lathes.

・The overall length is optimized for each machine manufacturers model, therefore no need to reduce the length of the tool.
・Intermediate diameters, such as the 2.5 mm I.D., 3.5 mm, 4.5 mm, have also been added. Not only Micro-Mini Twin but also small diameter boring bars can also be mounted.
・Four notches for clamping also allows for side fixation.
With Coolant Hole
Sleeve inner diameter : 3 mm-12 mm
Functional length 67 mm, 80 mm, 85 mm, 110 mm, 115 mm
Without Coolant Hole
Sleeve inner diameter : 2 mm-12 mm
Functional length 67 mm,80 mm, 85 mm, 110 mm, 135 mm
PVD Coated Grades for High Precision and Small Parts Machining MS9025
Effectively reduces notch wear whilst also providing fracture resistance.
High Al-rich (Al, Ti)N Single Layer Coating Technology
High Al and Conventional Coating Comparison
The high Al-rich (Al,Ti)N single layer coating provides stabilisation of the high hardness phase and succeeds in dramatically improving wear, crater and welding resistance.
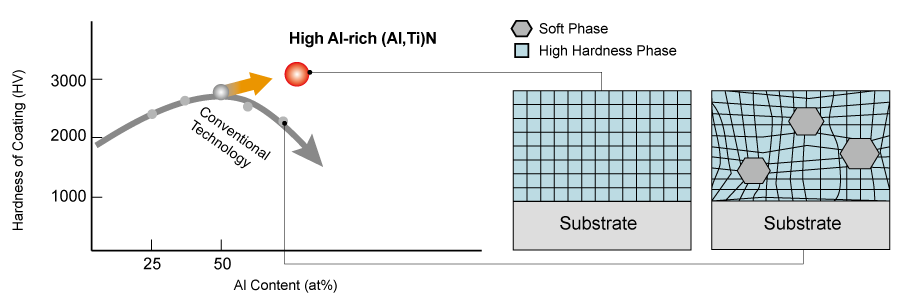
Smooth Surface of The Coating
The even surface of the coating has been achieved by first making the the carbide substrate smooth, then by promoting straight growth of the coating crystals.
This leads to excellent welding resistance.
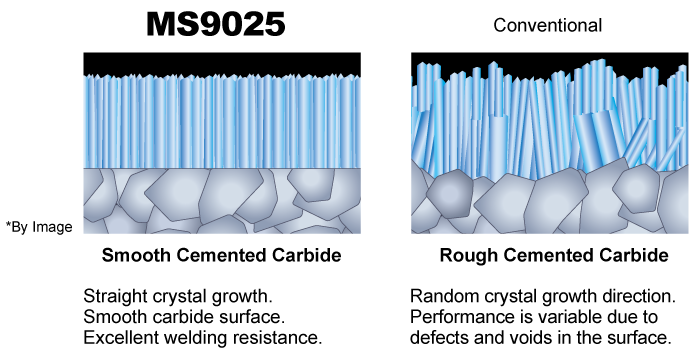
PVD Coated Grades for High Precision and Small Parts Machining MS7025
Dramatically improved welding and wear resistance in low feed machining with a more precise nano-multilayer coating
Nano-Multilayer Coating
By combining the high lubrication layer with excellent welding resistance, and the high hardness layer with a greater wear resistance that suppresses the progress of wear at the nano-level, the film damage is significantly reduced and the welding and wear resistance are dramatically improved.
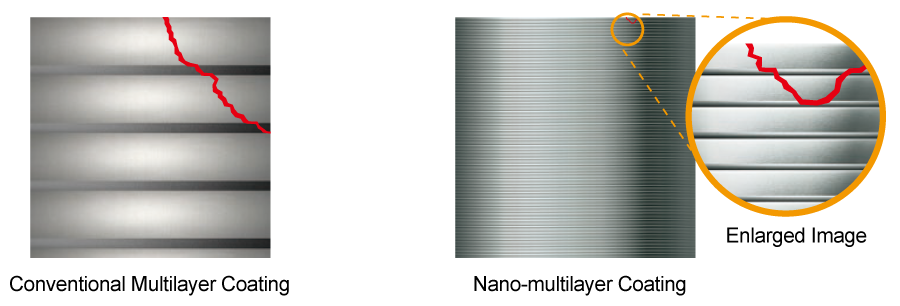
Effects of the High Lubrication Layer
The nano-level, high lubrication layer suppresses built-up edge caused by chip welding which tends to occur in low feed machining and in addition reduces on the machined surface.
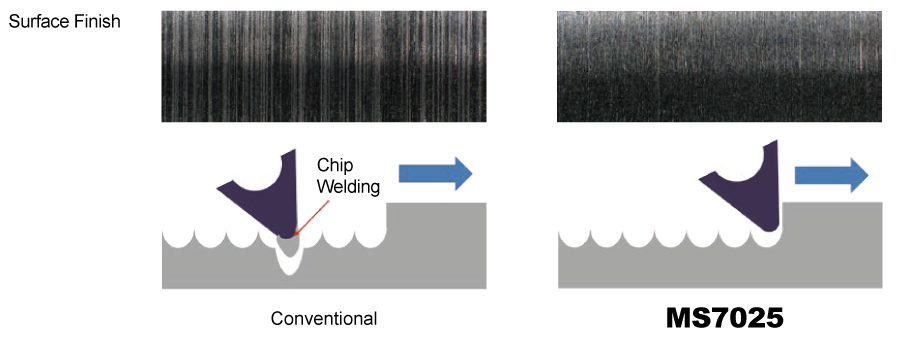
Technical consultation from here
24/7Contact form