MS6015 / MS7025 / MS9025
Classes com cobertura PVD para usinagem de peças pequenas e de alta precisão
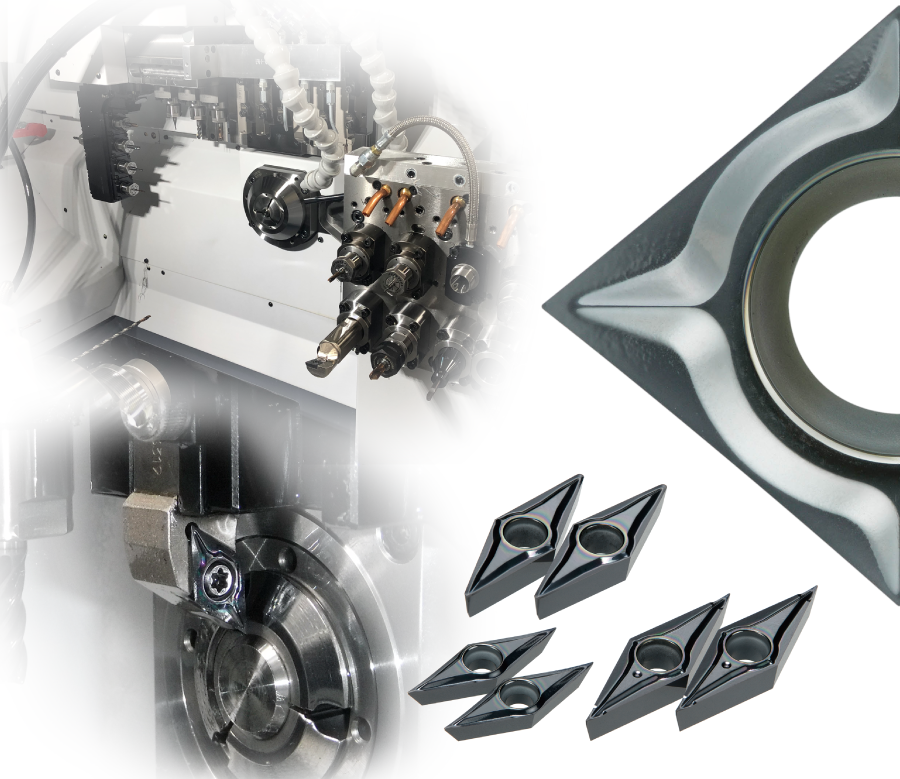
Contemporary Machining of High Precision Small Parts
MS7025
Dramatically improved welding and wear resistance in low feed machining with a more precise nano-multilayer coating
Nano-Multilayer Coating
By combining the high lubrication layer with excellent welding resistance, and the high hardness layer with a greater wear resistance that suppresses the progress of wear at the nano-level, the film damage is significantly reduced and the welding and wear resistance are dramatically improved.
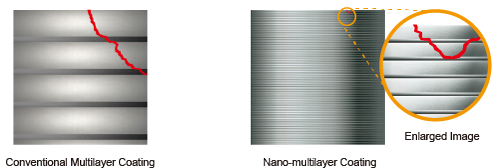
Effects of the High Lubrication Layer
The nano-level, high lubrication layer suppresses built-up edge caused by chip welding which tends to occur in low feed machining and in addition reduces on the machined surface.
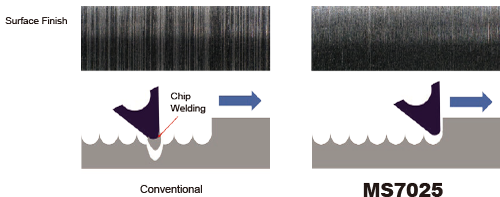
Comparison of End Face Machined Surfaces Using 3D Analysis
Achieves stable machining even during end face machining where the cutting speed is liable to change.
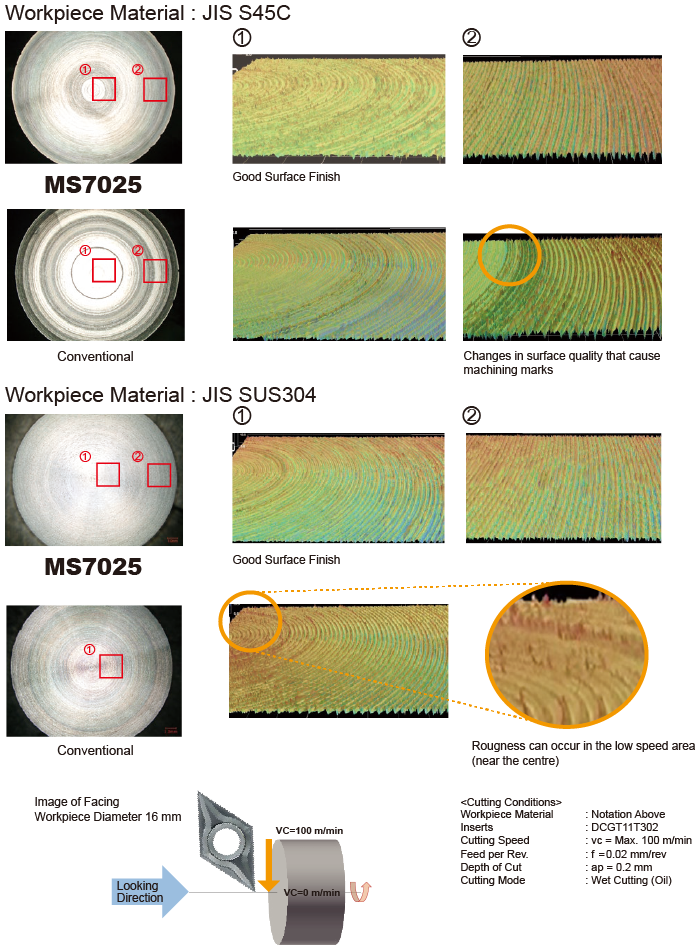
Effects of the High Lubrication Layer
The nano-level, high lubrication layer suppresses built-up edge caused by chip welding which tends to occur in low feed machining and in addition reduces on the machined surface.
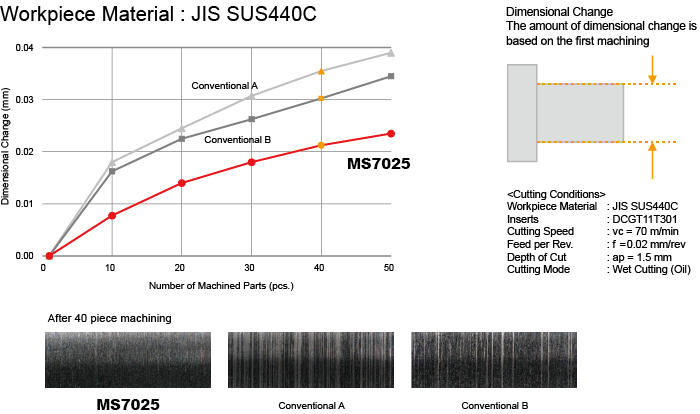
MS9025
Effective reduction of notch wear with a balance of wear and fracture resistance.
Improved Cemented Carbide
Thermal conductivity has been improved by optimising the grain size and therefore reducing the boundary
contact between the WC particles. This optimisation reduces the temperature of the cutting edge during
machining.
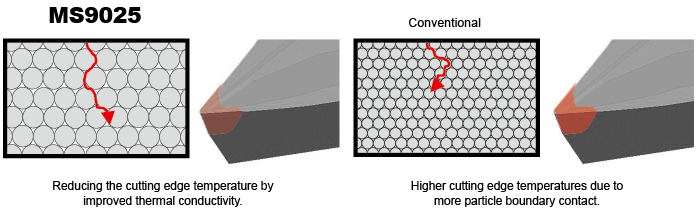
Smooth Surface of The Coating
The even surface of the coating has been achieved by first making the the carbide substrate smooth then by promoting straight growth of the coating crystals. This leads to excellent welding resistance.
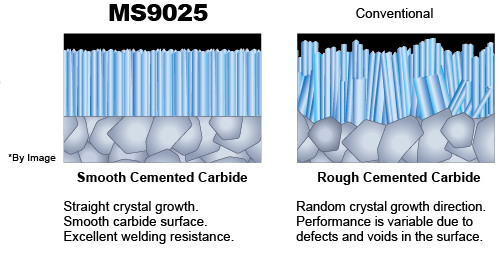
High Al-rich(Al,Ti)N Single Layer Coating Technology
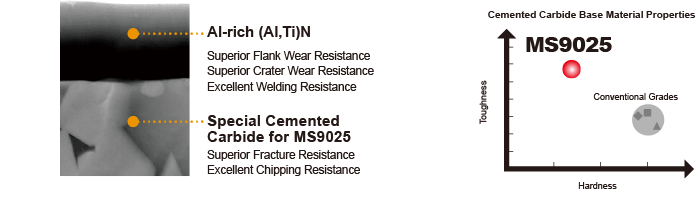
MS6015
Ideal for turning pure iron, carbon and free cutting steels whilst also providing excellent dimensional accuracy and good surface finishes.
Optimising the Laminated Structure
Optimising the laminated structure enables the hickening of coating which leads to significant wear resistance.
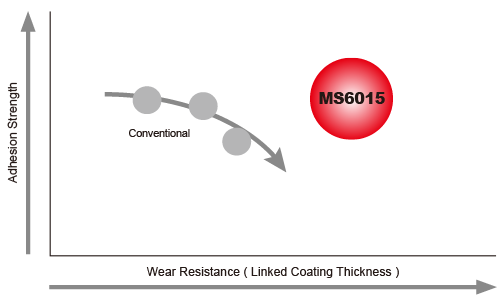
Ideal Inserts for Turning Small Parts.
Set the corner radius to a minus tolerance.
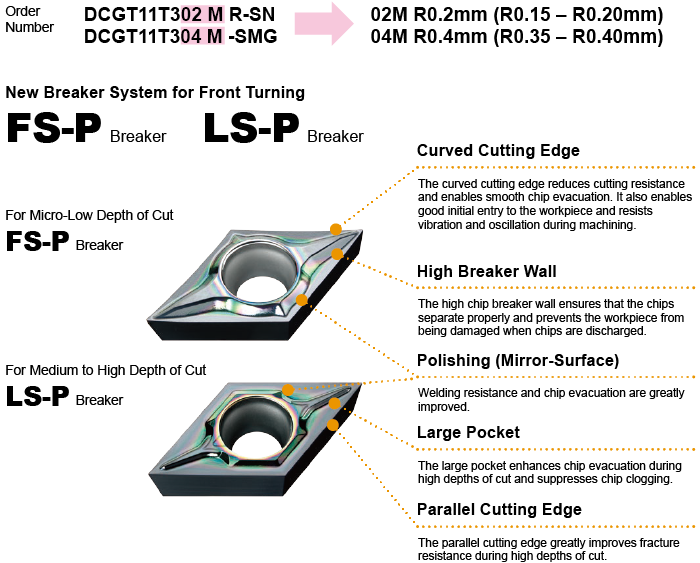
Extremely High Quality Cutting Edge
Technology that provides superior dimensional stability and reduces burrs.
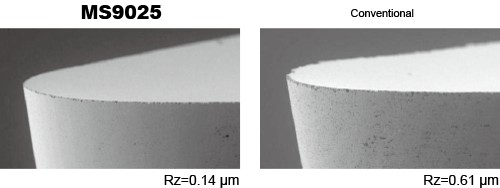
New Technology - Controlled Vibration of the Cutting Tool
Using new machine technology to deliberately vibrate the tool in relation to the cutting direction is an effective way of breaking chips.
This reduces production costs by reducing chip entanglement.
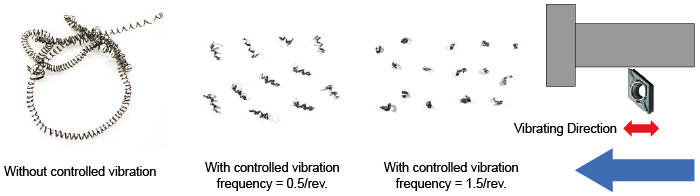
Challenges of controlled vibration machining:
Compared to standard machining there is a greater chance of edge chipping due to the extra stress on the cutting edge and also because of the impact of work hardening.
Benefits of using MS9025 for Controlled Vibration Machining
- Excellent fracture resistance due to the inherent toughness of the base material.
- Effectively suppresses boundary wear damage during machining of difficult-to-cut materials. This is achieved by the optimised cemented carbide grain size that reduces thermal conductivity and heating of the cutting edge.
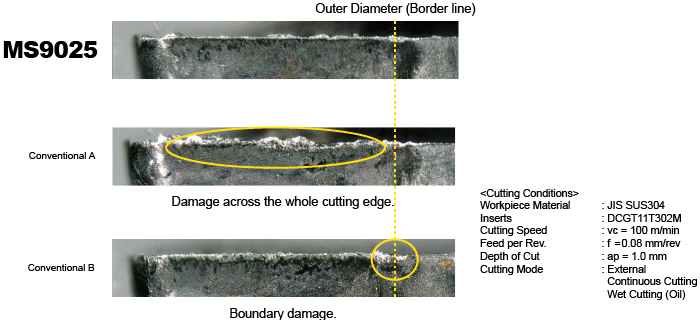
Application Examples
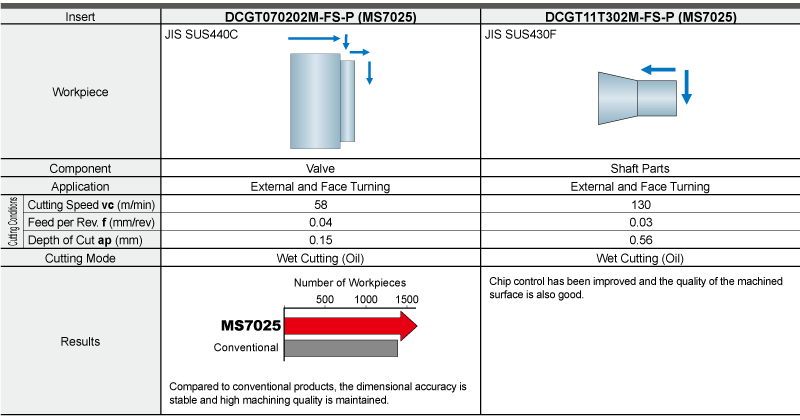
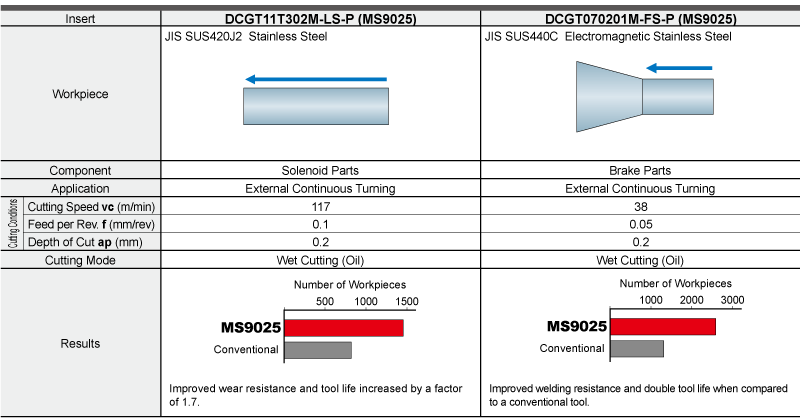
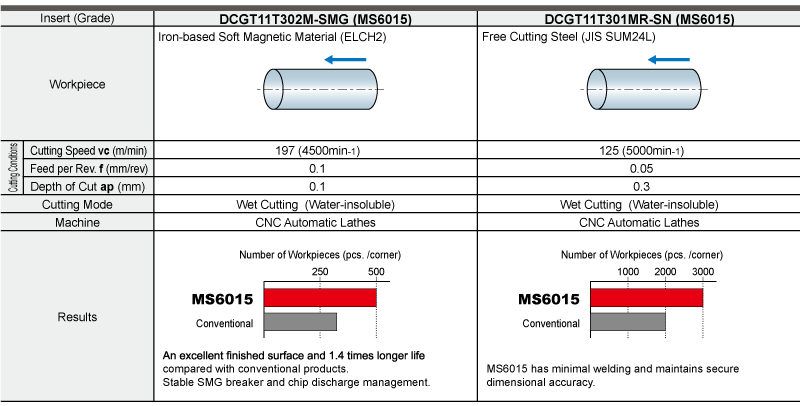
Fale conosco
Formulário para contato